Home >> Blog >> Wave Springs Pack More Force Into Less Space
Wave Springs Pack More Force Into Less Space
In many applications, flat wire wave springs offer significant advantages over traditional spring designs such as coils and discs.
Tried and true coil springs and disc springs work well in many engineering applications. However, it pays to compare these familiar options to another innovative spring design—flat-wire wave springs. Depending on the application, single- and multi-turn wave springs can offer distinct advantages over their more traditional counterparts.
Two of the most compelling reasons to specify wave springs involve force considerations including an impressive force-to-work height ratio and the ability to provide consistent force over a wide range of deflections. Other key advantages such as axial and radial space savings, absence of torsional loads, improved dimensional tolerances and increased travel make these unique wave spring elements clear winners in a wide variety of engineered systems and challenging work environments. For example, single-turn wave springs often replace stamped wave washers in applications from fluid power seals to noise attenuators. Multi-turn wave springs typically replace stacked disc springs or coiled springs in both power transmission and fluid power systems.
Here’s a closer look at the important technical benefits of wave springs and some applications in which wave springs shine:
Wave Springs Provide Consistent Force Over a Wide Range of Deflections
The ability to make fine linear adjustments across the entire force range is a key benefit of wave springs. Compared to coil or disc springs, wave springs offer deflection curves with a wider and flatter linear force region. Due to this unique design feature, wave springs have a linear force between 30 and 70% deflections, making it easier to meet specific spring force requirements. Coil and disc springs fall short in this regard due to significantly narrower linear force regions. Consider a few examples where this feature is especially useful:
Fishing Reels. Because wave springs require half the axial space of equivalent coil designs, reel assemblies can save on both weight and space, resulting in a more comfortable user experience and less fatigue. In addition, wave springs offer precise load deflection that enables a consistent spring rate and load progression over the targeted compression range. When used in a reel assembly, this consistent spring force allows the reel to operate smoothly and eliminate drag. In contrast, coil springs start out linear and then plane up at the end of the drag curve, which means the final 30% of drag adjustments are not possible. Using a wave spring offers finer control with a more linear curve—resulting in smoother drag and better performance.
Gear Sets. Within a gear set, using a wave spring will allow linear adjustments over the entire force range. In contrast, coiled spring designs can only enable fine linear adjustments at the beginning of the force range.
Slip Clutches. When using a slip clutch to extend the life of other machine components, it is critical for the clutch to react quickly based on preset torque values. Because wave springs offer the ability to make extremely fine linear adjustments, the slip clutch maybe set to promptly engage once the specified torque is reached.
Flow Valves/Safety Valves. Flow valves and safety valves must open in a reliable and repeatable manner at predefined pressure points. Wave springs make this possible by enabling fine and accurate linear adjustments.
Quick Connectors. Bayonet style connectors and other
quick connectors need to open at preset, safety critical
torque values. Wave springs may be used in these
designs to provide accurate linear adjustments that
prevent such connectors from opening prematurely.
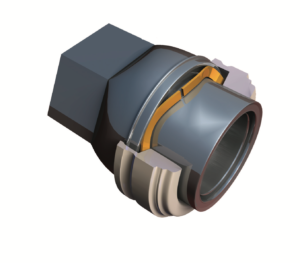
Wave Springs Save Space and Require Less Machining
Axial space savings are perhaps the most visible feature of wave springs when compared side by side with other spring designs. For example, in static applications, wave springs typically require only half of the work height of equivalent coil springs. This work height advantage falls to roughly one third in dynamic applications, due to the need for more turns to handle the bending stresses of a dynamic application. In either case, single- and multi- turn wave springs offer significant space savings over coil and disc designs. Consider that just one multi-turn wave spring can replace multiple coil springs in a traditional seal design. In addition, wave springs can save radial space compared to using disc and coil springs with larger diameters. The following are a few examples where space constraints are easily satisfied by specifying wave springs:
Mechanical Seals. These ubiquitous components are often used for sealing rotating shafts against stationary housing in equipment such as pumps and agitators. Sliding components are pressed against each other by force commonly generated by coil springs, which prevent the seal from opening on its own. In a wide range of seal applications, wave springs offer several benefits over coil springs. Beyond space savings, no additional holes are required in the seal housing to make room for wave springs. As a result, less machining is needed.
Another benefit is that wave springs can only compress axially, which means that no torsional loads are generated. In contrast, coil springs suffer from torsional loads that can cause preloaded components to rotate during use and lead to excessive wear and a decreased working load. A very low spring rate with an extremely flat load deflection curve can be achieved by using a multi-turn wave spring to prolong the life of a mechanical seal. Compared to disc springs that can cause massive wear due to edge contact, wave springs feature wide radial walls plus shim ends to offer a large supporting surface. Construction details are another edge: Wave springs are made from one piece of wire, so multiple springs are not necessary. Further, wave springs have no welding points that can break off during dynamic stress—a common occurrence with welded and stamped washers. For seals that require corrosion resistance, stainless steel and other materials such as Hastelloy C276 may be specified.

Downhole Tools. Spiral wound, multi-turn wave springs can be used to preload the anchoring devices of downhole tools used to bite into the casing bore once the tool has been actuated. Here’s how it works:
After the anchoring device has a good bite in the casing, a load must be applied to the heel of the slips to keep them
from de-energizing due to motions that occur during applied loads to the tool. Coil springs are traditionally used to apply this load, but multi-turn wave springs with crest-to-trough designs are a better alternative in many cases. Significant axial space can be saved by specifying wave springs, leading to more compact tool designs and reduced material costs. Besides the space savings, wave springs provide a more consistent load during the required travel versus conventional coil springs. Alloys such as Inconel and Elgiloy are available as wave spring materials for environments that encounter high temperatures and corrosive elements.
Wave Springs Manage Targeted Loads in Tiny Spaces
Certain applications are too small to make room for traditional coil springs, which can be somewhat bulky. In such cases, wave springs are useful for applying required preload in the tiniest of spaces.
Ultrasonic Motors. Motors that measure just millimeters in length are used in a wide range of applications, from the autofocus of a camera lens to automotive headrests and mirrors. Sophisticated surgical instruments and robotic devices commonly employ small motors as well. Let’s consider the ultrasonic motor used in the autofocus feature. In this application, a single-turn wave spring is used to maintain pressure against the stator, holding the rotor in place without using screws or bolts. For this miniature system, the wave spring is a better option than a coil or disc design, due to its low weight, compact size and ability to manage low to medium loads.
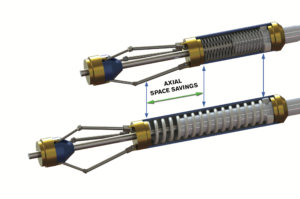
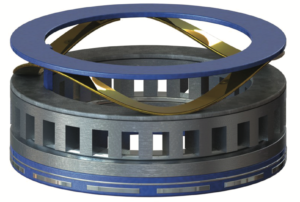
Wave Springs Can be Used to Preload Bearings, Reduce Endplay, and Minimize Vibrations
Applying a permanent thrust load to a bearing assembly is important for a secure and successful installation. The bearing preload process extends component lifetimes by eliminating unnecessary clearances, creating high stiffness and reducing noise and vibration.
Diesel Engine Water Pumps. Centrifugal impeller pumps are often used in large diesel engines such as those on locomotives. Over the past several years, incremental improvements have been made to increase service life and reduce pump maintenance. Using wave springs instead of coil or disc springs has proven to be an effective way to help maintain bearing performance and extend overall pump life. Here, the wave spring is mounted within the pump housing, around the shaft, and engages the housing and drive end of the impeller’s outer race bearing. The preloaded wave spring helps reduce the large thrust loads experienced by the tapered roller bearing by absorbing some of the reverse thrusts. In addition, the wave spring helps secure the bearings in place and reduce potentially damaging vibration.
Fluid Power Assemblies. Within hydraulic systems, retaining rings are often used to secure the cover element and eliminate the need to weld or screw components into place—leading to faster and easier field repairs. Using a wave spring between the cover element and inner tube will preload the inner components against each other and eliminate axial play. Eliminating this type of excessive movement helps to extend component and assembly lifetimes.
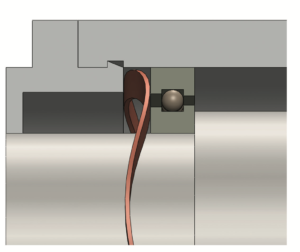
Read about The Best Springs You Haven’t Tried Yet.
To learn about selecting the correct products for your operating environment please contact your local Daemar Technical Sales Representative.